RECLAIM will deliver the first high-tech portable robotic MRF that can be used by waste management companies, demolition companies, local authorities and contractors. And Robenso has a huge role in it!
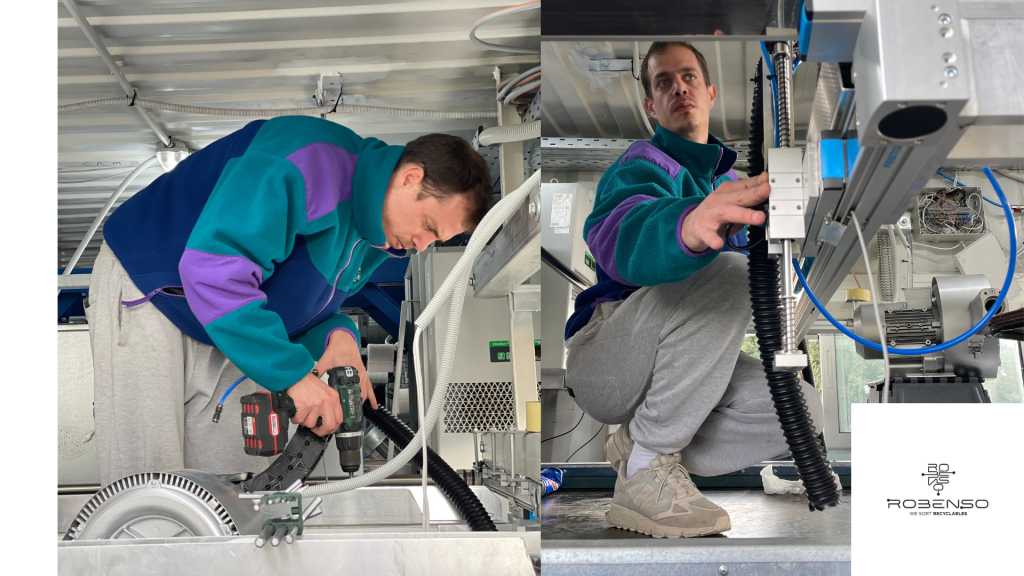
When Fredy from Robenso told us he and his colleagues spent 6 straight days with the prMRF container in Crete, we wonder if it was the sun, the sea, or just endless supply of souvlaki keeping them busy on the island. Not sure what we mean? Just see this LinkedIn post from some weeks back.
“I am happy to tell you that we finished the modifications to maximise the efficiency of the prMRF,” he informed us over a call.
Naturally, we asked him about the modifications, and how they improved the overall performance of the portable robotic material recovery facility (prMRF).
“We replaced the 3 DOF (Degrees of Freedom) system with an optimised 2.5 DOF version. We upgraded the vacuum generator by installing a new blower, valve, and filters, making the machine more powerful and reliable.”
And just like that, we walked right into his tech trap.
But in plain terms, shifting from 3 DOF to an optimised 2.5 DOF delivered immediate results:
- Sorting success increased from 75% to 98%.
- Picks per minute jumped by 10%, from 22 to 25.
- Since the new system required fewer motors, Robenso now has the option to add another robotic sorter for increased efficiency, a decision that will be made at a later time.
This image slider below shows three different robotic sorters: 1.5 DOF, 2.5 DOF and 3 DOF, respectively.
Robenso’s intervention comes at a critical time for the RECLAIM project, as the prMRF is now deployed in the target island of Kefalonia in Greece. Prior to this, the prMRF was publicly showcased for the very first time at Verde.tec expo in Paiania, Greece. In the next 6 months, the consortium-wide brain power will bear fruit.
More importantly, this will be the first time since project inception that the prMRF will be undertaking material recovery operations with real waste streams, and its operations will be closely monitored via a LIVE web-based interface to perform adjustments on the go.
Reaching this technological readiness level (TRL) wasn’t as measured and precise as the robots sorting waste inside the prMRF.
In fact, Robenso’s journey within the EU-funded Reclaim project has been anything but a linear, upward curve, and punctuated with numerous challenges. Not nearly as fun if everything were simple, right?
Folks at Robenso, especially Fredy and Nikos, love to spend a lot of time with the prMRF, and our project coordinator Michalis Maniadakis from Forth-Hellas was quick to capitalise on this rather odd but completely valid enthusiasm: “This is a good way to make people work on Saturday’s and Sunday’s,” chuckled Michalis, who takes his jokes very seriously. Don’t believe us, take a look here in the comments section.
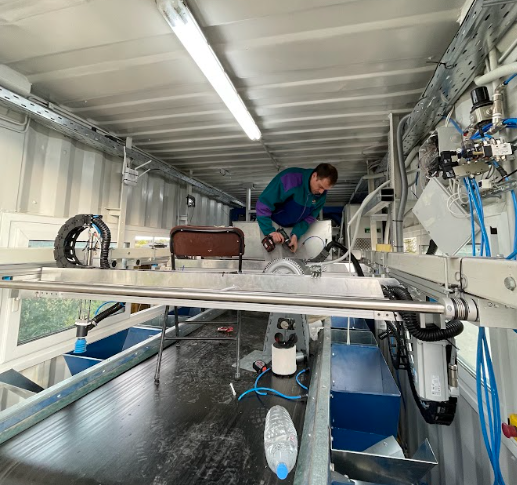
Developing a cost-effective sorting solution for Reclaim
Jokes aside, Robenso was uniquely aware from the start that to tackle the robotic sorting problem, existing systems used by other companies offered some answers. Many were using Delta robots, which are widely used in industries like pharmaceuticals and food due to their precision in robotic picking. But there was a major issue—”they’re expensive and patented, meaning you need special permission to use them,” said Fredy.
From the get-go, the consortium knew that just a sorting machine won’t do.
Robenso had to be realistic, which meant creating a cost-effective robotic solution that would have a sustainable place in the waste industry, particularly in lower-budget markets like developing countries.
The first solution: 1.5 DOF Linear Sorter
“We scratched our heads for a while and eventually landed on a linear sorting system,” Fredy explained.
This is what we call a 1.5 Degrees of Freedom (DOF) machine—it moves freely along the X-axis and has limited up-and-down motion along the Z-axis. The movement works with a hybrid approach:
- X-axis movement is fully controlled by an electric servo motor.
- Z-axis movement is pneumatic, meaning it can only move up or down.
So, here’s the punchline: The combination works well because the servo motor provides precise control, while pneumatics keeps costs low.
“This gave us a machine that was simple and effective, but it wasn’t perfect.”
The limitations of 1.5 DOF: No real-time object tracking
While this machine could reliably sort waste at a decent speed, Robenso ran into a big problem—it couldn’t track objects in real time while picking. That meant sorting accuracy wasn’t as high as they wanted, especially when compared to Delta robots.
As the Reclaim solution is aimed at local municipalities as one of the end-users, understandably, they would want a guarantee that waste residues will be minimal.
“Since we couldn’t provide that with the 1.5 DOF system,” Fredy said, “we had to make improvements.”
The upgrade: 2.5 DOF with tracking ability
To solve the tracking issue, Robenso developed a 2.5 DOF system. This version was similar to the original but with one key improvement: It synchronises the suction cup’s velocity with the conveyor belt, allowing for real-time tracking during sorting.
The result?
Sorting efficiency jumped from 90% to 98%.
The challenge with 3 DOF robots and how Robenso fixed it
For some context, let’s rewind to 2022.
Reclaim initially had plans to employ a hybrid robotic approach focusing on efficiency and cost-effectiveness. That is, the project would use three different types of robots, including three 1.5 DOF (translates as “Degree of Freedom”, indicating the range of robotic movement) for high volume sorting early in the process, one 2.5 DOF robot for better accuracy in later stages, and one 3 DOF robot for full freedom to move anywhere on the conveyor belt (along X, Y and Z axes).
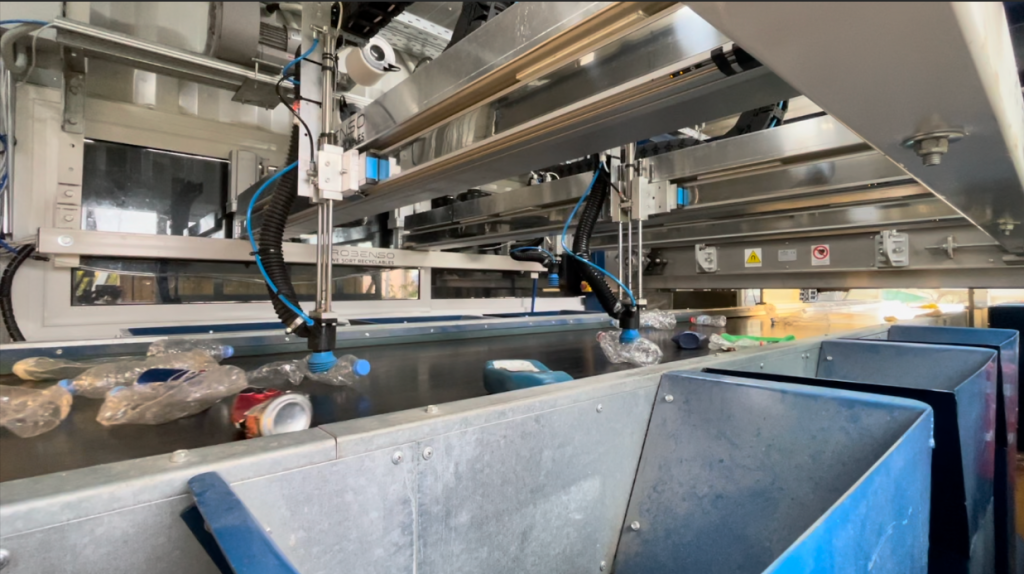
But, here’s the thing: while the 3 DOF robot was designed to test grippers from KU Leuven and handle more complex sorting tasks, it turned out to be costly, bulky and complex to implement.
“We want to be able to host more weight like: finger grippers, Havco grippers, eject grippers from KUL but also test pneumatic driven vacuum generators that are fitted on the end effector (XYZ video) so we made the 3 DOF XYZ robot. We did many tests and we found really promising results basically for all those grippers but the sorting rate was slow due to the heavy duty structure and the pneumatic driven vacuum source drained our resources,” said Fredy.
So, to deliver a more industrial machine at Kefalonia, Robenso transformed it to 2.5 DoF where it gained 10% better sorting rate by making it lighter.
“We also gained from 75 to 98% sorting success by upgrading the vacuum system with an electric blower as the pneumatic driven vacuum playing at a sustainable (for the air compressor) rate was low,” added Fredy.
“The 3 DOF robot needed many servo control motors for movement along the conveyor belt. But more importantly, during testing, it didn’t perform as expected,” said Fredy.
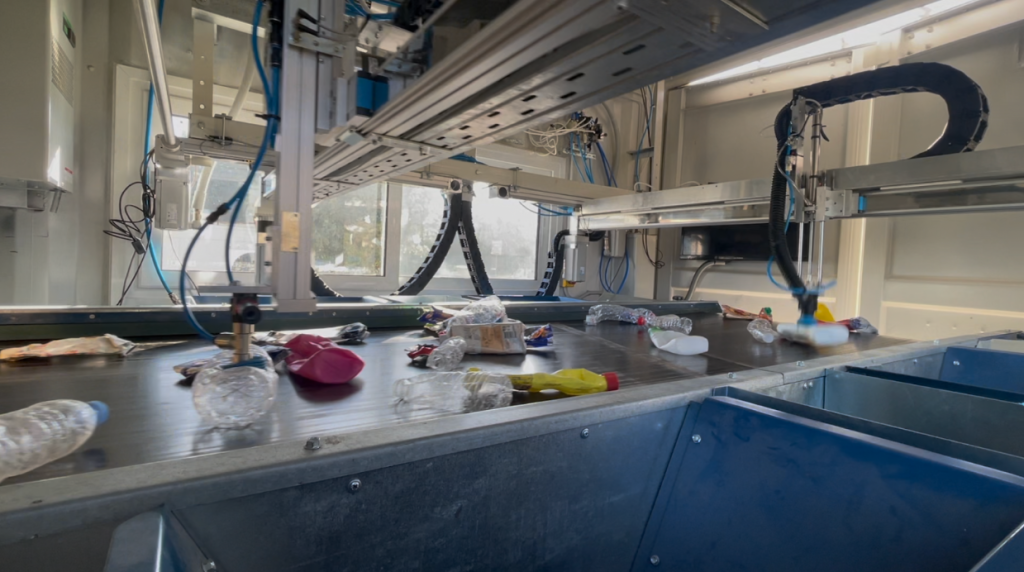
“When HERRCO came in for testing, we realised the 3 DOF robot was slow and inefficient, mainly due to the vacuum generator. It required a huge amount of compressed air, which drained resources from the other robots,” he added.
So, this idea was axed.
Cut to 2025, an optimised 2.5 DOF robot was developed in its place, as mentioned earlier in the article, lightening the construction and accelerating the process. Additionally, by upgrading the vacuum system, the overall functionality was significantly improved.
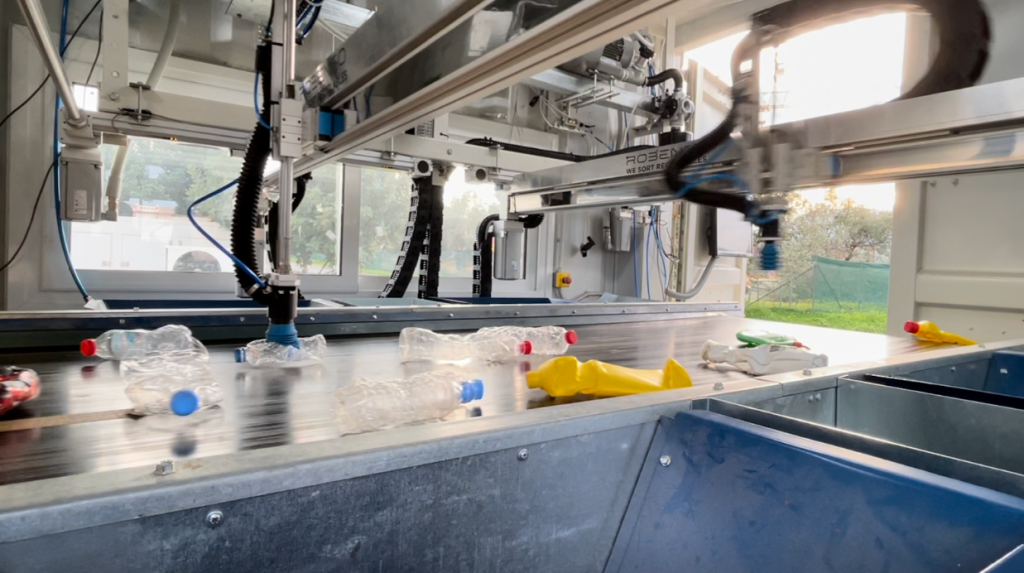
Speaking of robotic waste sorting, RECLAIM project uses Robotic Recycling Workers (RoReWos) that have the potential to be the new trend in the area of robotic material recovery.
They are low-volume, low-cost, modular, high performance robots with interchangeable grippers able to recover a wide variety of materials from waste streams and deposit them to material-specific bins. The use of RoReWos is expected to significantly increase cost-efficiency and productivity in material recovery facilities.
The future of decentralised material recovery: Smarter, faster sorting
Overall, the whole process of developing a robotic sorting system has been about balancing performance and cost. The linear sorting robots offer a scalable, affordable solution, while the 2.5 DOF upgrade provides the tracking ability needed for higher efficiency. By making the right trade-offs, RECLAIM project is closer to a mass-deployable, cost-effective sorting solution for waste management—one that can work in both urban and remote settings.